The A400M (formerly known as the future large aircraft) is a military transporter designed to meet the requirements of the air forces of Belgium, France, Germany, Spain, Turkey, Luxembourg and the UK.
A European staff target was drawn up in 1993, together with a memorandum of understanding signed by the governments of the seven nations. Italy subsequently withdrew from the programme.
Image @abc.es
Airbus Military SL of Madrid, a subsidiary of Airbus Industrie, is responsible for management of the A400M programme.
Other companies with a share in the programme include BAE Systems (UK), EADS (Germany, France and Spain), Flabel (Belgium) and Tusas Aerospace Industries (Turkey). Final assembly took place in Seville, Spain.
A400M future large aircraft programme
Image @nbcnews.com
In May 2003, a development and production contact was signed between Airbus and OCCAR, the European procurements agency, for 212 aircraft. France, Germany, Italy, Spain, the UK, Turkey, Belgium, and Luxembourg initially signed but Italy subsequently withdrew. The order was consequently reduced to 180 aircraft with deliveries starting in 2009. These will continue until 2020.
First metal cut for the airframe of A400M was in January 2005 and assembly began in 2007. The first flight was scheduled for early 2008; however, development problems with the engines caused this to be postponed. The first aircraft was officially rolled out in June 2008 and the long-awaited A400M took its maiden flight on 11 December 2009.
The aircraft took off with 127t in weight, carrying 15t of test equipment, including 2t of water ballast. Its official maximum take-off weight is 141t.
Source: EADS. Graphic: Cristina Rivera Gª, Dept. of Computer Graphics.
1 | Flight refueling probe | 62 | IFF antenna |
2 | radome | 63 | Front side of the center wing box |
3 | Weather radar | 64 | Costilla central wing box |
4 | Forward pressure bulkhead | 65 | Centr fuel tank drawer. |
5 | Localizer antenna and glideslope | 66 | Clamping elements wing / fuselage |
6 | Rudder pedals | 67 | Cuadernas |
7 | Navigation instrument panel | 68 | Accom. the main landing gear |
8 | Control Units | 69 | Main Landing Gear |
9 | central pedestal and levers engine | 70 | Lever-type dampers |
10 | Passenger seat | 71 | multidisc carbon brakes |
eleven | Windshield | 72 | Trapdoor main landing gear |
12 | HUD projection system data | 73 | wing fuel tanks |
13 | the third crew member workstation | 74 | Fuel pumps |
14 | Pilot seat | 75 | Fixed trailing edge wing |
fifteen | Third crew member seat (m. Tactics) | 76 | Antifreeze pipe system |
16 | top panel | 77 | FRONT anchor. the nacelle |
17 | Sidestik | 78 | Anchoring engine nacelle under wing |
18 | Steering wheel nose wheel | 79 | Front side of the outer wing |
19 | side console | 80 | rear engine mount frame |
twenty | 4th folding seat crewman | 81 | fire wall |
twenty-one | Storage space | 82 | Capots engine |
22 | Rest area of the flight crew, two bunks | 83 | Direction of rotation of the propellers |
2. 3 | Emergency escape hatch | 84 | RATIER-FIGEAC propeller blades 8 |
24 | Door of the cockpit | 85 | Feathering system |
25 | Kitchen | 86 | Turboprop Europrop (10,000 hp) |
26 | Storage space | 87 | propeller gearbox |
27 | IFF antenna | 88 | accessory gearbox |
28 | Electronic equipment cabinet | 89 | Nozzle |
29 | Stairs | 90 | Pod refueling |
30 | Avionics compartment | 91 | Navigation light left |
31 | Floor beams support | 92 | radar system |
32 | Since the loadmaster | 93 | Aileron |
33 | electronics compartment under the floor | 94 | Fuel tank ventilation |
3. 4 | Front landing gear | 95 | Aileron actuator |
35 | Hatches front landing gear | 96 | outer flap |
36 | Front sensor missile alerter | 97 | inside flap |
37 | Drawer front landing gear | 98 | Backdoor paratrooper |
38 | Crew normal access with integrated ladder | 99 | hydraulic tank |
39 | Frame, supporting structure of the door | 100 | lifeboat |
40 | Oxygen bottles | 101 | flaps hydraulic motor |
41 | front window | 102 | Auxiliary Power Unit (APU) |
42 | Oxygen generation system | 103 | Access APU maintenance |
43 | Obs light. leading edge | 104 | Escape from the APU |
44 | Troop seat | 105 | Cowling behind. union wing-fuselage |
Four. Five | Cargo handling rollers | 106 | Emergency escape hatch |
46 | Emergency door | 107 | hydraulic actuator ramp |
47 | Bunk beds for evacuation | 108 | Ramp extensions |
48 | TACAN antenna | 109 | Portalón |
49 | SATCOM antenna | 110 | Stabilizer main drawer. vertical |
fifty | Landing Light | 111 | rudder onesie |
51 | Carena left | 112 | Rudder actuators |
52 | Sinker wind generator. | 113 | HF antenna |
53 | Conditioned air mixer. | 114 | Vertical-fuselage stabilizer clamping |
54 | Conditioned air duct. | 115 | Compensator horiz stabilizer. |
55 | Conditioned air group. left. | 116 | adjustable horizontal stabilizer |
56 | Air vent | 117 | Elevator |
57 | Air intake | 118 | Stable fastening pivot. horizontal |
58 | Antenna V / UHF | 119 | anti-collision light |
59 | Heat Exchanger | 120 | spoiler |
60 | TACAN antenna | 121 | Cone rear fuselage |
61 | lifeboat | 122 | Self-protection equipment |
Source granadahoy.com
In January 2009, EADS postponed the first deliveries of the A400M until 2012, and proposed to develop a new approach for the A400M to discover new ways to advance the programme.
2009 continued to be a troubled year for the A400M as estimates on the cost overrun of the project were released with predictions of up to €11.2bn over budget. The South African Air Force started to look at alternatives to the A400M and the European partners placed it under consideration. Airbus suggested that the programme may be scrapped unless €5.3bn could be provided.
In November 2010, Belgium, the UK, France, Germany, Luxembourg, Spain and Turkey agreed to lend Airbus €1.5bn and proceed with the programme; however, Germany and the UK reduced the number of aircraft ordered to 53 and 22 respectively, decreasing the total to 170.
First deliveries were made to French Air Force in August 2013. Deliveries are expected to conclude in 2025.
A400M test flights
Image @thalesgroup.com
This first A400M is known as MSN1. The second A400M, MSN2, completed its maiden flight on 8 April 2010, while MSN3 completed its maiden flight on 9 July 2010. The fourth A400M MSN4 completed its maiden flight in December 2010. The first production aircraft of A400M (MSN7) completed its maiden flight on 6 March 2013.
The development of the A400M fleet was designated as Grizzly in July 2010. Trials with MSN1, MSN3 and MSN5 are performed in Toulouse, while those with MSN2 and MSN4 are done in Seville, providing greater flexibility and taking advantage of the best weather conditions available.
The A400M was displayed at two events in 2010: the Berlin Air Show in Germany, and the Farnborough International Airshow in the UK.
In October 2011, A400M was tested on wet runways and taxiways. The water ingestion test was completed successfully. The latest cold weather tests were concluded in February 2013.
Engine problems ground German A400Ms
Germany has grounded two of the three Airbus Defence and Space (DS) A400M transport aircraft that it has so far received following the discovery of excessive engine wear, national media disclosed on 30 June.
Flight operations of aircraft 54-01 and 54-02 – the first two received in December 2014 and December 2015 – have been temporarily suspended after inspections found heavy engine wear after only 365 and 189 hours of operations respectively, Der Spiegel reported, adding that engine wear on the third aircraft, 54-03, had also been identified.
This issue is likely to be connected to problems that were identified with the EuroProp International (EPI) TP400-D6 engine earlier this year. In April it was reported that engines were being affected by excessive abrasive wear and heat resistance. It was noted that parts of the engine were struggling to stand up to the extreme temperatures, with individual components found to be flawed. A UK Royal Air Force aircraft suffered an in-flight engine shutdown as an apparent result of these issues.
At that time Airbus DS said that it was working hard to solve the issue of excessive abrasive wear, noting that it “has no impact on the security of the plane”.
It is understood that the issue has been isolated to the propeller gear-box (PGB); the part that converts the rotating high-speed motion of the engine into a slower speed motion for the propeller. A significant number of engines that are both on the final assembly line (FAL) and in service have had to be replaced because of quality issues, though the issue affects only gearboxes with a clockwise rotation.
EPI has performed an analysis of the issue, identified the root cause, and developed a procedure whereby each gearbox is inspected every 200 hours. If a crack is found the gearbox is then inspected every 20 hours after that to keep the aircraft that have been delivered flying. Gareth Jennings, London – IHS Jane’s Defence Weekly 01 July 2016 Source janes.com
A400M orders
Total firm orders for the A400M stand at 174 aircraft. Malaysia ordered four and 170 aircraft were ordered by seven countries, including the UK (22), Belgium (7), Turkey (10), France (50), Germany (53), Luxembourg (1) and Spain (27).
C-130J Hercules: Details
MP14-0471 C-130 5723 Israel Ferry. Lockheed Martin Aeronautics Company, Marietta, Ga. Lockheed Martin Photography by Todd R. McQueen
In April 2005, South Africa signed a contract with Airbus Military to be a full participant in the A400M programme. South Africa ordered eight aircraft, for delivery between 2010 and 2014. South Africa then cancelled the order in November 2009. In December 2005, Malaysia signed a contract for the purchase of four A400M.
Airbus could ask for bail-out due to A400M military plane: Here
Excerpt
Airbus could ask for a bail-out from Britain and other countries buying its A400M military transport aircraft after take a massive hit on the project.
The pan-European aerospace company’s annual results showed Airbus took a €2.2bn charge because of problems with the A400M, with chief executive Tom Enders calling renegotiations of the contract.
And here’s a cool video filmed by Ben Ramsey who got a great close-up footage!
A400M design
The A400M has a much larger payload than the C-160 Transall and C-130 and the design makes extensive use of composite materials. The capability for short, soft field landing and take-off is part of the requirement and the aircraft has six-wheel high-flotation main landing gear.
The need for airdrops and tactical flight requires good low-airspeed flight and the aircraft also has long-range and high-cruise speed for rapid and flexible deployment.
A400M HIGH LIFT CONTROL & MONITORING SYSTEM
- Complete in-house development of both hardware and software, including application software
- Both SW and HW certified in accordance with RTCA DO-178B/-254 DAL A
- Control-, monitoring-, autonomous- and electronic maintenance functions for the High-Lift System
- Sensor inputs for determination of actual flap position and shaft speed
Source saab.com
Final assembly of the composite (carbon-reinforced plastic – CRP) wingbox is taking place at Airbus UK in Filton. GKN Aerospace in the UK has supplied the complex carbon composite wing spars. Denel Aviation of South Africa is the supplier of the fuselage top shells and wing-fuselage fairings. EADS, Augsburg, is supplying the 7m × 4m composite cargo door.
Fuselage assembly is at Airbus Deutschland in Bremen, Germany. Final assembly of the A400M aircraft takes place at EADS CASA in Seville.
APU (APS 3200)
The APU, to be supplied by Hamilton Sundstrand Power Systems of San Diego, California, will be a derivative of the reliable APS 3200 unit, which is the standard fit APU for the Airbus single-aisle programme. The A400M APU, mounted in an upper wing fairing, will provide pneumatic power for starting the main engines and will also provide electric and pneumatic power for operation of aircraft systems and air conditioning when the engines are not running. Source flightglobal.com
APS 3200 unit
Ram Air Turbine (RAT) emergency power system
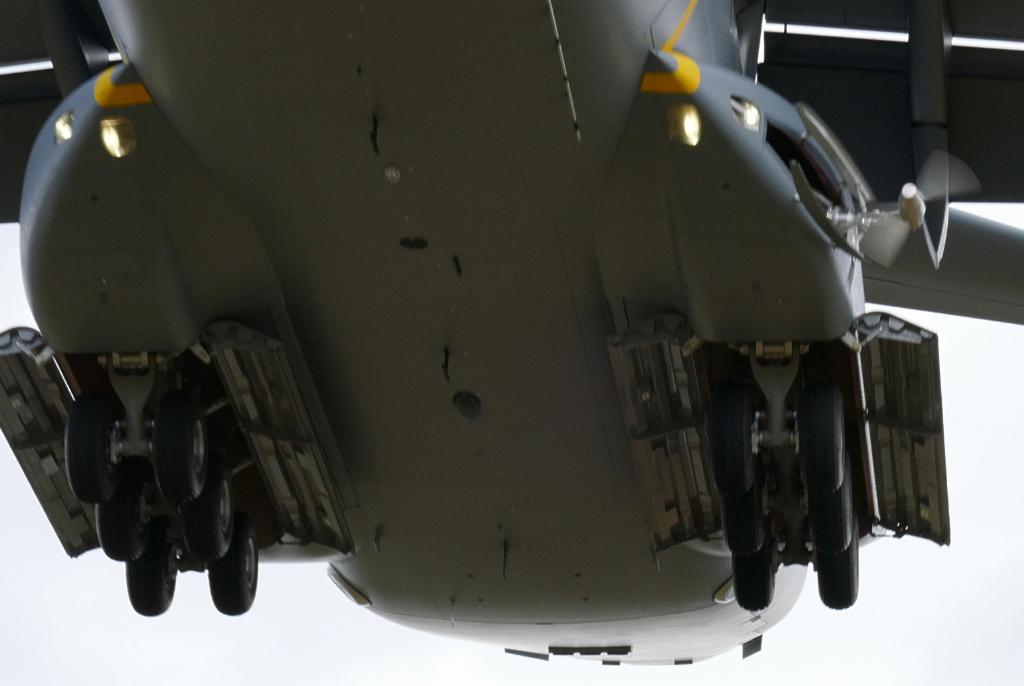
Example of RAT – Image @enseeiht.fr
The RAT provides 45 kVA of electrical power to critical loads in the event of a total power loss.
Source prnewswire.com
Cockpit of the military transporter
The cockpit is fully night-vision compatible and provides accommodation for two pilots and an additional crew member for special mission equipment operations. It is fitted with a fly-by-wire flight control system developed for the Airbus range of civil airliners.
Two sidestick controllers are installed to allow the pilot an unrestricted view of the electronic flight displays. The throttle controls are placed centrally between the two pilot stations.
Thales and Diehl Avionik Systeme are developing the A400M’s FMS400 flight management system, based on integrated modular avionics modules, an adaptation of systems being fitted on the Airbus A380 airliner.
The avionics includes cockpit control and display systems with nine 6in × 6in displays and a digital head-up display which features liquid crystal display (LCD) technology and enhanced vision systems (EVS), for enhanced situational awareness, automated CG calculation, automated defensive aids systems, simple EMCOM switching, simplified switching, uncluttered screens, automated tanker and receiver fuel control and auto fuel tank inerting.
‘RMP’ and P.A. communications equipment for the A400M model
Cobham Avionics (TEAM) has been chosen as the supplier for Airbus Military for the A400M programme relating to PA and RMP communications equipment. Source europavia.es
The A400M for Germany is fitted with a terrain-masking low-level flight (TMLLF) system, from EADS Military Aircraft, for low-level flight control. The TMLLF system has a Saab Avitronics flight computer. EADS Defence & Security Systems digital map generator is also fitted.
There is a military mission management system (MMMS), from EADS Defence Electronics, which includes two mission computers. The MMMS controls cargo handling and delivery, calculating the load plan and the computed air release point before an air drop, as well as fuel management and fuel operational ranges. The MMMS also manages the tactical ground collision avoidance system (T-CGAS) and military / civil communications.
Rockwell Collins was selected to supply the HF-9500 high-frequency communications system and the avionics full-duplex ethernet (ADFX). Cobham Antennas Division provides the SATCOM antennas.
HF-9500 Airborne Communication System
Rockwell Collins’ HF-9500 airborne communication system features digital signal processing technology that delivers high-quality, reliable performance for military fixed-wing airborne applications. This 400-watt, single integrated system solution is designed to satisfy current and future high-frequency (HF) voice and data communications requirements.
As an integrated, multi-mode system, the HF-9500 provides data communications capability over HF to modems, video imaging systems, secure voice devices, teletype and data encryption devices. It delivers the superb HF voice communications capability and reliability that our customers expect from the Rockwell Collins HF family.
Features & Benefits
- Exportable worldwide
- Automatic link establishment offers best clear-channel selection
- Digital signal processing
- Global range and 400 watts of power ensure continuous tactical communication
- Embedded data modem
- Upgradable to meet future requirements
- Filtering for Simultaneous Operation (SIMOP) applications
Source rockwellcollins.com
Countermeasure technology
The EADS Defence Electronics defensive aids suite includes an ALR-400 radar warner from Indra and EADS, MIRAS (multicolour infraRed alerting sensor) missile launch and approach warner developed by EADS and Thales, and chaff and flare decoy dispensers. A laser DIRCM (directed infrared countermeasure) system may be added later.
ALR-400 radar warner
The ALR-400 is an advanced radar warning system developed specifically for the Airbus A400M tactical military transport aircraft. ALR-400 would be able to effectively detect any incoming radar-based threat. The system is being produced by a team comprising EADS Defense Electronics and Indra of Spain.
ALR-400 radar warner, defensive aids computer, MIRAS multi-color missile warner and a chaff/flare dispenser are the basis for the A400M aircraft self-protection system which is expected to achieve initial operational capability by 2010 with 85 systems on order to equip the same number of A400Ms. Source deagel.com
The aircraft can also accommodate armour plating crew protection, bulletproof windscreens, engine exhaust treatment for infrared emission reduction and inert gas explosion retardation and fire retardation in the fuel systems. The wings have hardpoints for the installation of electronic warfare pods and refuelling pods.
A400M transporter cargo systems
Rheinmetall Defence Electronics is supplying the loadmaster control system for electronic cargo control. Loadmaster consists of a workstation and control panel, eight sidewall lock panels and a crew door panel. It provides efficient ground loading and airborne cargo drops.
Loadmaster Workstation (LMWS)
The loadmaster uses the Loadmaster Workstation (LMWS) to finalize the load and trim sheet required for takeoff, which was prepared with the MPRS and transmits it electronically via an aircraft server to the cockpit, where it is printed and signed. This is one of the few remaining paper formats still existing in the A400M system.
New ground is broken when it comes to the responsibilities of the loadmaster: The A400M loadmasters are to accomplish not only logistical, but also technical tasks on the aircraft in future.
Particularly the technical part presents new challenges in the fields of personnel selection and training. In simple terms, the technical qualification of the loadmasters will conform with the EASA CAT A level; thus, jobs up to maintenance level 1 (onboard) can be carried out.
This approach requires a completely new training cycle: Depending on the previously acquired technical skills, e.g. the Air Forces Engineering schools will provide an “EASA CAT A equivalent delta training course.” Subsequently, the A400M loadmaster type rating course will take place – the traditional loadmaster training course on the A400M aircraft as well as the “Maintenance Course for Loadmasters.”
Building upon the CAT A knowledge, the latter will convey A400M-specific contents. Thus, the loadmaster will become capable of conducting “ground handling and servicing”, simple troubleshooting and maintenance activities.
Source eatc-mil.com
Image @defenceindustrydaily.com
The payload requirements include a range of military helicopters and vehicles, heavy engineering equipment, pallets and cargo containers.
The cargo bay can transport up to nine standard military pallets (2.23m × 2.74m), including two on the ramp, as well as 58 troops seated along the sides or up to 120 fully equipped troops seated in four rows. For Medevac, it can carry up to 66 stretchers and 25 medical personnel.
Right dropping door and wind deflectors used during the jump
The A400M can carry 116 paratroops and air-drop them and their equipment either by parachute or gravity extraction. It can air-drop single loads up to 16t; multiple loads up to 25t total; 120 paratroops plus a wedge load of 6t, or up to 20 1t containers or pallets.
It can also perform simultaneous drops of paratroops and cargo (RAS / wedge or door loads) and very-low-level extraction (VLLE) of a single load up to 6.35t, or multiple loads up to 19t total weight. Gravity extraction can be performed for a single load up to 4t, or multiple loads up to 20t total weight.
The cargo compartment can be configured for cargo, vehicle or troop transport or air drop, a combination of these and for aero-medical evacuation. A single loadmaster is able to reconfigure the cargo compartment for different roles either in flight or on the ground. A powered crane installed in the ceiling area of the rear section of the fuselage has a 5t capacity for loading from the ground and for cross-loading.
The rear-opening door has full compartment cross-section to allow axial load movement, roll-on and roll-off loading and for the air drop of large loads.
A400M tactical tanker and refuelling
The A400M is convertible to a tactical tanker, with the ability to refuel a range of aircraft and helicopters within two hours. Flight Refuelling Ltd is supplying the 908E wing pod drogue system, which provides a fuel flow of up to 1,200kg/min for each pod, plus the centreline pallet-mounted hose drum unit fitted in the rear cargo bay, which provides a fuel flow of 1,800kg/min.
908E wing pod drogue system
908E Wing Dispense Equipment (WDE)
Flow rate Up to 400USgpm
Weight Up to 630kg wet
Delivery pressure 50psig
Hose length 80ft trailed length
Operating envelope Fixed wing 180 – 300kts
Rotary wing 105 – 130kts
Source cobham.com
The A400M can now refuel fighters and transports from underwing pods, but helicopter stability in trail has proved problematic. A longer hose may be the solution. – ainonline.com
In addition, up to two cargo bay fuel tanks (CBT), which connect directly to the A400M’s fuel management system, can be fitted. Total fuel capacity is 46.7t or 58t with the CBTs.
Airbus A400M Atlas Airborne Refuelling Chart
In October 2011, GKN Aerospace won the £6m ($9.54) contract from Cobham Mission Equipment. It includes supplying air refuelling pylon for A400M. It also supplies a wing spar for the A400M.
Navigation
The aircraft’s independent navigation system comprises an inertial reference system (IRS) integrated with a global positioning system (GPS). The weather and navigation radar is the Northrop Grumman AN/APN-241E, which incorporates wind shear measurement and ground mapping capability.
Northrop Grumman AN/APN-241E
The only radar in the transport class with a high resolution SAR mapping mode
The AN/APN-241’s capability remains unmatched by the competition as the only radar in the transport class with a high resolution SAR mapping mode. In addition to meeting needs for precision navigation, this unparalleled mapping capability enables operators to execute landing missions with confidence on unimproved runways without aid from ground-based landing systems.
No other radar in the industry can compete with the range and accuracy of the AN/APN-241. It is the only radar with a 10nm range Windshear mode and its unique two-bar can technology eliminates false alarms. And, unlike other systems, the AN/APN-241 windshear mode is not restricted by altitude. At 20 nautical miles, the AN/APN-241 provides the longest range air-to-air situational awareness mode of any transport radar. The Skin Paint mode also features computer generated target-sizing, a clutter-free display, and hands-free operation to the crew.
Simultaneous multifunction capability
The AN/APN-241 is designed to allow pilots to focus on the mission rather than “working” the radar. Automatic tilt and gain adjustments reduce operator tasking, and with simultaneous mode interleaving, crews can select independent radar modes according to mission requirements. The AN/APN-241 provides overlays of flight plan or TCAS information on weather or ground maps for greater situational awareness. Operators may also ‘freeze’ the AN/APN-241 into a non-emitting mode to gain a tactical advantage.
The AN/APN-241 was built with growth in mind. Modifications to current modes and technologies will provide a maritime patrol capability suitable for fisheries protection, smuggling interdiction, and Search and Rescue missions. With the development of ‘Ballistic Wind’ mode, a modification which will measure drop zone winds, the AN/APN-241 provides a unique air drop capability to support both military and humanitarian missions.
Proven versatility
The highly adaptable AN/APN-241 is currently fielded on four aircraft: C-130H, C-130J, C-27J and C-295. Northrop Grumman has integrated the AN/APN-241 with five different avionics architectures and two antenna systems. As the baseline radar for the LMCO C-130J and Alenia C-27J, it has a solid, long-term production base with logistics and maintenance support through 2030 and beyond.
Source northropgrumman.com
General data: | |
---|---|
Type: Radar | Altitude Max: 0 m |
Range Max: 64.8 km | Altitude Min: 0 m |
Range Min: 0.4 km | Generation: Early 1970s |
Properties: Pulse-only Radar |
Sensors / EW: |
---|
Generic Doppler Navigation/Weather – Radar Role: Radar, Weather and Navigation Max Range: 64.8 km |
Source cmano-db.com
The radio navigation suite includes a pair of instrument landing systems, VHF omnidirectional radio ranging (VOR), radio distance measuring equipment (DME), air traffic control (ATC) transponders, automatic direction finders (ADF) and a tactical air navigation unit (TACAN).
Engines onboard the A400M
In May 2003, Airbus Military selected the three-shaft TP400-D6 turboprop engine, to be manufactured by EuroProp International (EPI). EPI is a consortium formed by Rolls-Royce (UK, Germany), ITP (Spain), MTU (Germany) and Snecma (France). Rolls-Royce is responsible for overall integration.
EuroProp International (EPI) TP400-D6 engine
The development of this advanced military turboprop engine is shared by ITP, MTU Aero Engines, Rolls-Royce and Snecma. The partners have launched a joint company, Europrop International (EPI), to develop, manufacture and support the TP400-D6.
The TP400-D6 powers the A400M military transport which has successfully completed its maiden flight in Spain’s Seville in late 2009. The TP400-D6 successfully entered into service with the French Air Force in late 2013.
MTU is responsible for the TP400-D6’s intermediate-pressure compressor, intermediate-pressure turbine and intermediate-pressure shaft and has a stake in the engine control unit. Furthermore, final assembly of all TP400-D6 production engines takes place at MTU Aero Engines in Munich and acceptance testing at MTU Maintenance Berlin-Brandenburg. Source mtu.de
TP400-D6 engine
- Power range in excess of 11,000 shp
- Low risk design and life cycle cost
- Low susceptibility to FOD and erosion
- Ample growth potential
The TP400-D6 is a collaborative engine between Rolls-Royce, MTU, Snecma and ITP. The engine was designed to fulfil the European Staff Requirements (ESR) for the A400M military transport, an aircraft used for peacekeeping missions abroad.
Within the collaboration, Rolls-Royce areas of responsibility include overall engine performance, Air & Oil systems, Intermediate casing, 6-stage High Pressure Compressor and the Low Pressure shaft.
Rolls-Royce is contracted to development and production of more than 750 engines for the A400M fleets of Germany, France, the United Kingdom, Spain, Turkey, Belgium and Luxembourg, and the production of additional engines for potential export customers.
Specification | TP400-D6 |
Power (shp) | 11,000+ |
Bypass ratio | 0.8 |
Pressure ratio | 25 |
Length (in) | 137.8 |
Diameter (in) | 36.4 |
Basic weight (lb) | 4,026 |
Compressor | 5IP, 6HP |
Turbine | 1HP, 1IP, 3LP |
Applications | Airbus Military A400M |
*Technical data (ISA SLS)
Data rolls-royce.com
The four engines each have a maximum output of more than 11,000shp. EPI states they are the largest turboprops ever made in the West. The engines are fitted with FADEC (full authority digital engine control), supplied by BAE Systems and Hispano-Suiza.
Eight-bladed composite variable pitch FH386 propeller
Image @ainonline.com
Ratier-Figeac SA of France (a business unit of US-based Hamilton Standard) supplies the eight-bladed composite variable pitch FH386 propellers. The propellers are 5.33m (17.5ft) in diameter and fully reversing with the capability to back the fully loaded aircraft up a 2% slope. FiatAvio supplies the propeller gearbox.
Electrical power generation systems are supplied by Aerolec, a joint venture between Thales and Goodrich. The variable frequency generators will provide up to 400kVa.
Operational range
Operational range of A400M with 20-tonne (44,000 lb) and 30-tonne (66,000 lb) payloads, flown from Paris, France. source wikiwand.com
Image @wikimedia.org
Landing gear
Messier-Dowty was chosen as the supplier of both main and nose landing gear. Each main landing gear consists of three independent twin-wheel assemblies, providing six wheels on each side. This allows the plane to land on unprepared runways. The landing gear system also enables the A400M to ‘kneel’ which lowers the rear ramp to facilitate the loading of large vehicles.
The main landing gear shock absorbers maintain a minimum distance from the ground whatever the load. Messier-Bugatti supplies wheels and brakes. The aircraft has two nose wheels and 12 braked wheels.
EuroProp International (EPI) has developed TP400 power plant for the A400M. The power plant has been installed on the inner engine mount of the C-130K flight test-bed.
The A400M’s normal operating speed is 555km/h, but it can reach a maximum speed of 780km/h. The normal and ferry ranges of the aircraft are 3,298km and 8,710km respectively. The service ceiling is 11,300m.
The take-off and landing distances of the aircraft are 980m and 770m respectively. The aircraft weighs around 76,500kg and the maximum take-off weight is 141,000kg.
Main material source airforce-technology.com
Main image by Martyn William’s Aircraft @flickr
Updated Jan 30, 2018
Type |
Military transport aircraft |
Engine |
4 × Europrop TP400-D6 turboprop, 8,250 kW (11,060 hp) each |
Altitude |
11,278 m max. |
Producers |
France, Spain, Germany, Italy, United Kingdom, Belgium |
Operators |
Germany, France , Spain, United Kingdom, Turkey, Belgium, Luxembourg, Malaysia. |
Armament |
No armament, cargo transport |
Performance |
Maximum speed: 780 km/h |
Take Off Weight |
141,000 kg |
Avionic |
EADS Defence Electronics defensive aids suite, ALR-400 radar, EVS enhanced vision systems, automated CG calculation, DIRCM (directed infrared countermeasure), |
Dimensions |
Length: 45.1 m; Wingspan: 42.4 m; Height: 14.7 m |
Technical data airrecognition.com